The development stage is one of the most significant steps in the entire manufacturing process. During this stage, engineers and designers can work out any errors, inconsistencies, or failures in the machine before full development.
When manufacturing a medical device for patient safety, development is a priority. Because of this, the U.S. Food and Drug Administration (FDA) has set forth standards regarding medical device use and safety.
These standards should make it easier for manufacturers to build prototypes that adhere to medical safety to ensure these devices act as intended.
The Medical Device Safety Act was introduced in the U.S. in 1990.
Enacted to enhance public protection and patient safety, the act states that the FDA must be notified when any medical product causes illness, injury, or death to an individual. Broadly, it’s a type of medical device patient safety act intended to limit the negative impacts of poor device manufacturing.
Upon such notification, the FDA takes action to track or possibly enact device recalls for these products. Because of this act, hospitals and other health care facilities are required by law to report to the FDA any manufacturer of any medical devices not adhering to device safety and effectiveness testing.
In this way, organizations can do their part to maintain healthcare device safety through Medical Device Act adherence.
- Breakdown of Key Medical Device Standards
- Standards & Practices in Medical Device Testing
- Standards & Practices in Medical Device Usability
What is Considered a Medical Device?
Per section 201 (h) of the Food, Drug, and Cosmetic Act, a medical device is “an instrument, apparatus, implement, machine, contrivance, implant, in vitro reagent, or other similar or related article, including a component part, or accessory.” which is recognized in the official National Formulary, or the United States Pharmacopoeia, or any supplement to them.”
The category includes everything from a gauze pad to the disinfectant used to sterilize an electronic medical device, like a monitor or keypad.
How Does the Medical Device Safety Act Affect the Prototyping Process?
The answer is, at the beginning. The FDA has five specific steps in the medical device safety development process:
- Device Discovery and Concept
- Preclinical Research-Prototype
- Pathway to Approval
- FDA Review
- FDA Post-Market Safety Monitoring
We will focus on the first two steps and their relevance to medical device use and safety.
Medical Device Discovery
The Federal Food, Drug, and Cosmetic Act, section 513, established a risk-based device classification system for medical devices. The various devices are classified differently during this initial stage of the process.
- General controls or Class I devices are the least risky for public health and include surgical tools, oxygen masks, etc.
- Class II devices pose more risk to the patient and therefore are subject to both general and special controls including specific performance standards and medical device safety testing.
- Class III devices involve the support or sustaining of life and are often implanted in the body, presenting a much more substantial risk to the patient. Because of this, Class III devices are subject to all ‘controls’ as well as pre-approval.
The manufacturers of these devices must prove the safety and effectiveness of the device. Therefore, Class II and Class III devices must adhere to stricter safety standards in the prototyping process.
Preclinical Research Prototype
Once a concept for a device is classified, manufacturers know what types of controls, pre-approvals, testing services, and safety standards they will need for full FDA approval.
From there they begin to build a prototype (not for human use!) utilizing ALL of these standards. These prototypes are each produced in controlled, laboratory settings. At this stage, again, using medical device safety standards and testing, manufacturers continually refine the prototype thereby learning more about its potential use in the health care industry.
Failure by manufacturers to adhere to the safety standards can delay the production process and possibly hinder public health best practices.
Developing a Production-Ready Medical Device Prototype
The professional manufacturer incorporates device testing services and safety standards during every phase of the prototyping process, ensuring a positive development timeline.
If a manufacturer dismisses specific medical device safety testing, a device may fail its usability testing and require reconfiguration and additional device testing.
In addition to the safety standards for the devices mentioned above, the medical safety device act requires that manufacturers maintain compliance with additional regulations including:
- IEC 62366
- IEC 60601
- IEC 60601-1
- IEC 60601-1-2
- IEC 60601-1-6
- ISO 13485
- ISO 9001
- ISO 14971
- FDA
When a manufacturer successfully develops a prototype that complies with safety standards and proves effective, they can approach the FDA to market the device.
The Importance of Safety Standards in the Prototyping Process
With over 250,000 deaths reported annually, medical device safety and standards have become more crucial than ever. Fortunately, safety and the Medical Device Act work in tandem with each other.
The global market of medical devices is large and complicated. RBC Medical Innovations specializes in helping medical device companies navigate this market and bring their products to the healthcare industry faster and with fewer delays.
Contact us today to learn how we can help you with your challenges in medical device manufacturing.
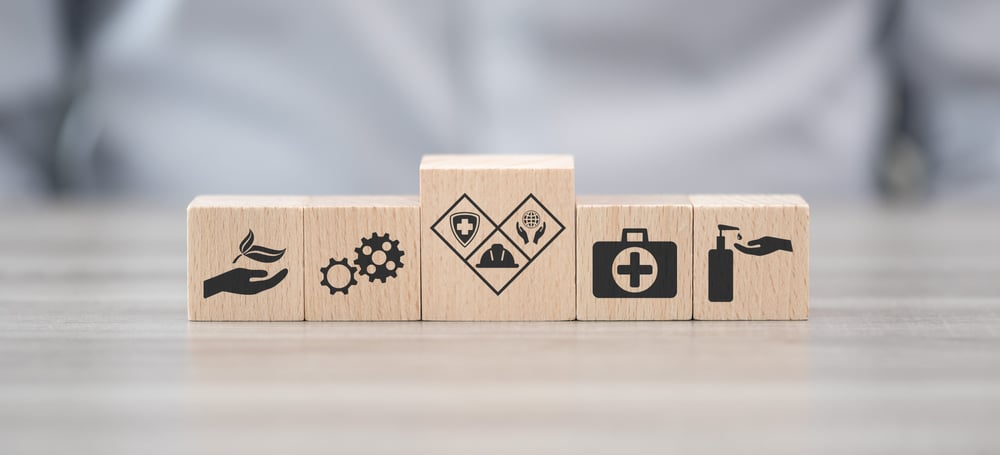
Approaching Medical Device Safety Standards Compliance
In the United States, medical device companies that manufacture, repackage, relabel, and/or import medical devices sold in the U.S. are regulated by the Food and Drug Administration’s (FDA) Center for Devices and Radiological Health (CDRH). To be cleared or approved for sale, devices must adhere to outlined medical device safety standards.
For many medical device companies, especially those that are just starting up, it is easy to feel overwhelmed or perhaps even nervous as they begin to learn the length of time it may take to receive FDA approval and the myriad of FDA medical device safety requirements they must adhere to. For example, a device in the design phase could have over a dozen medical equipment safety standards to follow.
Here are some tips to start your systematic approach to meeting medical device safety standards.
Outline your regulatory strategy. It is essential to evaluate and plan for regulatory considerations from the first day of your development process. Building a marketable medical device in the U.S. requires regulatory preparedness – in everything from your development to your documentation, to usability testing and using quality management systems, and finally your FDA submission package. Depending on the regulatory pathway your device requires, you may need to have formal or informal meetings with the FDA in your development process. Formulating a regulatory strategy can help you prepare for those meetings as well as inform other elements of your process.
Select a predicate device. Identifying a predicate device, one that is already on the market that is similar to yours, helps to refine medical device safety testing requirements and standards to follow during the design and development of your device. A Premarket Notification (510(k)) is a premarketing submission made to FDA to demonstrate that the device to be marketed is safe and effective by proving substantial equivalence (SE) to a predicate device that is not subject to Premarket Approval (PMA). Submitters must compare their 510(k) device to a similar legally marketed U.S. device(s). If the FDA cleared it already, they should evaluate it the same way as the existing device. If you struggle to pinpoint a single predicate device that operates in a similar manner as yours, you may be able to find pieces of those elements in multiple devices on the market. Then you can combine them and select the relevant standards to create a precedent for your process.
Pull together your list of relevant standards and determine what medical device safety testing is applicable. As with most projects, an important first step is to pull together your to-do list to fully understand what is coming on your regulatory pathway. The daunting list swirling around in your head of medical device safety standards may feel more manageable once you have it all together. It is also important to know that it may not be necessary for you to perform and pass all medical device safety testing outlined in each standard – you may be able to whittle down your list simply by evaluating what testing is actually needed for your device to be considered safe for both the operator and the patient.
Account for local deviations. No matter what regulatory body you are seeking approval from, each entity has their own deviations from the general medical device safety requirements that are based on specific needs or practices in the countries that they cover. For full device compliance, it is important to know and understand what they are.
Seek expert advice. Having the counsel of medical device engineering and regulatory experts will remove the uncertainty in following these steps. A consulting company can help you compile your comprehensive medical device safety standards list, establish the necessary testing processes, select the right predicate device or find a creative combination of parts in existing devices, and adhere to local deviations.If you are struggling with compliance to medical device safety standards and don’t know where to begin, Sterling can help. Our medical device development group addresses the whole development process, and our regulatory experts help our clients produce products consistent with the highest industry standards. If we can help you meet your medical device testing and standards goals, contact us today.